In order to achieve greater quality, efficiency and consequently achieve greater team performance, companies adopt different methodologies and resources that contribute to these factors.
Increasingly, companies are creating and applying a variety of programs, methods and practices, seeking improved results, cost reduction, waste elimination and comprehensive improvements.
If you are familiar with our blog, you will have already read about many of these methodologies adopted. Today we will talk about 5S: what is it, benefits and how to apply the methodology?
>> Read also: Kanban: what is this method and how does it work?

What is the 5S methodology?
The 5S methodology had its origins in Japan, after the Second World War. During this period, the country was in crisis. Therefore, it was necessary to find solutions to increase efficiency in the work environment and thus return to being a productive economy.
5S is a simple management program for companies. However, it is implemented with a lot of focus and determination to create a safe and pleasant place. In this sense, one of its principles is continuous improvement, so that its results are lasting and not momentary.
As a management tool for companies focused on improving areas such as organization, cleaning and standardization, the program takes its name based on five “s”. They are Japanese senses that translated are:
- Seiri – sense of utilization;
- Seiton – sense of organization;
- Seiso – sense of cleanliness;
- Seiketsu – sense of normalization;
- Shitsuke – sense of discipline.
First S – Seiri
The first S is the concept of sense of use. In this sense, the objective is to keep only what is necessary in the work environment. It is necessary to constantly evaluate the equipment in use. Identify the essential and the dispensable. This values the team's concentration and productivity.
Second S – Seiton
The second S is the sense of organization. After selecting what is useful and what is not, it is necessary to organize and categorize everything so that collaborators know where to find the materials.
Maintaining organization is essential so that there is no pollution in the work environment, making it uncomfortable and unproductive.
Third S – Sixo
Seiso is the sense of cleanliness. Here, team unity in keeping the work environment clean is valued. The interesting thing is that this responsibility is divided and not just delegated to the cleaning team alone.
Each person's personal image is also valued, without imposing dress or appearance standards. However, everyone is required to always be suitable for the work environment.
Room S – Seiketsu
The fourth S is the sense of standardization or normalization. This sense aims to make all others part of the company's routine, making them something automatic and a habit of the team.
Seiketsu serves so that everyone on the team can adopt the mindset of this methodology so that it really has an effect.
Fifth S – Shitsuke
This is the sense of discipline and self-discipline. It is the practice of the methodology without being charged by the board, it is the successful implementation of the management program.
5S is the union of these senses in favor of a goal achieved through all the practices mentioned. Thus, the program also becomes a style of thinking. In this sense, to be successful, everyone involved needs to have their senses in mind and ready to put them into practice.
>> Read also: Just in Time: concept, application and care
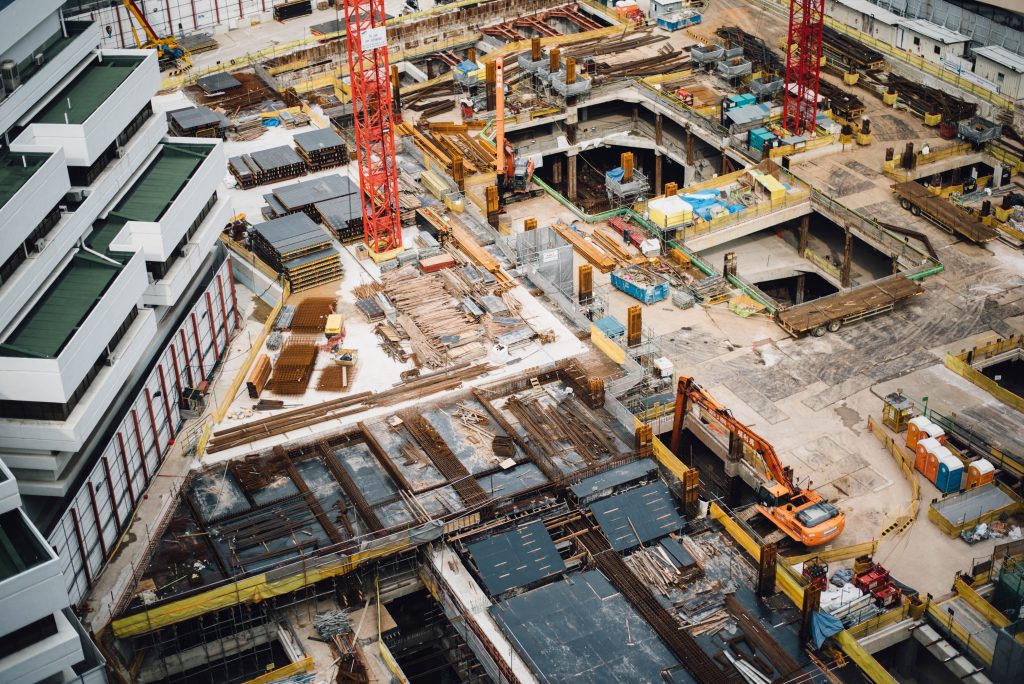
Benefits of 5S
The initial objective of the methodology was just to make the work environment a cleaner, more organized and functional place so that the work day could be more productive. However, today the methodology is also adopted to improve processes, control quality and increase employee productivity.
Let’s see some of the main benefits that this methodology brings:
time optimization
In an organized, clean and strategic work environment, workers have more time to invest in necessary things. This is because there will be no equipment, dirt, clutter, or other related distractions to interrupt the work.
Standardization
One of the senses is standardization. Through the union and daily practice of the methodology, processes become increasingly standardized, making the routine easier.
Waste reduction
With the first S, by selecting only materials that are used in everyday work and discarding what is not useful, it is possible to reduce waste, avoiding buying and keeping materials that are not used.
Service quality improvement
The combination of senses and their effects results in an improvement in the quality of the final delivery. Whatever it is, product, service or planning, if done in an environment in which this methodology is a lifestyle and something present, it will certainly have a good quality delivery.
>> Read also: Six Sigma: Understand what it is and what it's for

How to implement the 5S program
The big challenge here is not actually implementing the program, but maintaining it over time. Because despite requiring simple attitudes, to maintain them complicity and discipline are necessary.
company rating
To implement the methodology, it is necessary to assess which are the critical points in the company, and analyze which improvements that the program brings that are necessary, defining which areas have priority and need more attention.
Planning
In the planning phase, it is essential to select those responsible for teaching the methodology to the rest of the team, so that each one understands the methods and their participation in the application.
5S
At this stage, it is essential to involve all employees in the implementation of the program, starting from the first sense, applying one at a time, until reaching the last and applying continuous improvement, making the program a company philosophy and culture.
Focus to maintain the methodology
After implementing the program, it is necessary to maintain focus and discipline so that the actions become a habit, because at first it may seem very easy, but maintaining the routine of the methodology is one of the main challenges.
Results
Measuring the results is essential to know how much the methodology is having an effect, therefore, promoting periodic evaluations can be a good method of measuring the team's commitment level and the program's efficiency. It is also important to monitor changes in productivity, the working environment and the quality of service provided by employees.
Feedbacks
To motivate the team to continue living the 5S philosophy, it is necessary to show the results that the methodology adds.
For this, the team assigned to teach and implement the methodology must establish a feedback culture, showing which results are being obtained through new habits and which benefits these results add, both for the team and for each employee individually.
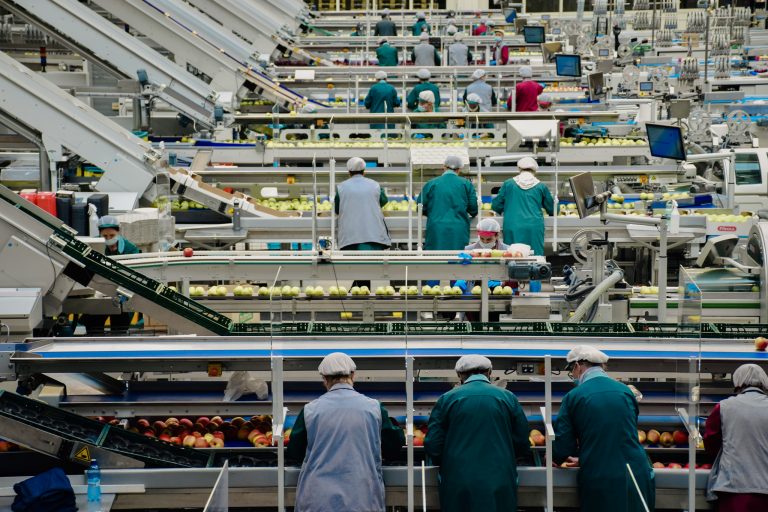
Extracting the best from your company!
The 5S program is perfect for making your company a more organized, safer and consequently more productive place.
Now you know what this methodology is, what the concept is, its benefits and how to apply it. Just follow the step by step and extract the best from your company!
And for that, if you want to improve the work environment by optimizing time, increasing productivity and reducing costs and waste, in addition to this methodology, you can bet on the system Manufatura 360!
It will bring you all these benefits and innovation through enabling technologies. Trust the most complete platform on the market to make your company more efficient!
Visit our website and talk to one of our experts to learn more.
If you liked this methodology and our content, also read the article on our blog “Lean Manufacturing”.